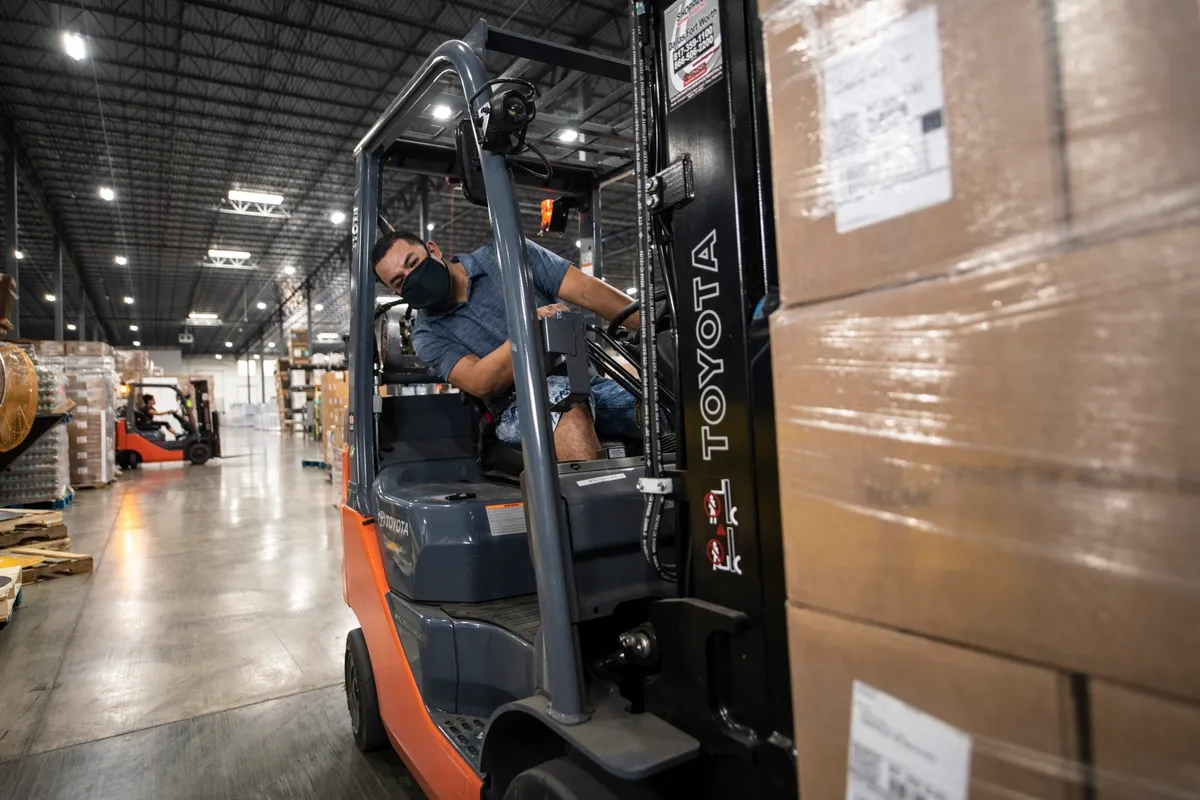
Material handling fleet managers are always seeking to drive down total operating cost for their operations. When considering how to power their fleets, fleet managers are pursuing high fleet and vehicle uptime, minimal operator intervention and time, minimal environmental impact, low maintenance and low infrastructure upgrades. While lead-acid-battery-powered vehicles - and the associated battery swapping rooms and processes - still dominate the market, forward-looking fleets are starting to adopt hydrogen fuel cells and lithium-ion batteries to lower their operating costs. In this blog post, we explore the benefits and costs for hydrogen fuel cells and lithium-ion batteries combined with automated wireless charging. We find that fleet managers can achieve the benefits of hydrogen with 50% lower upfront capital outlay and $5,000 per year per truck lower operating expenses by instead switching to lithium-ion batteries that are charged automatically and wirelessly.
Higher Energy Density and Efficiency
Lithium-ion batteries boast higher energy density compared to hydrogen fuel cells. This means they can store and deliver more energy in a smaller and lighter package. The efficiency of lithium-ion batteries is also superior, as the conversion of stored energy to power is more direct. In contrast, hydrogen fuel cells involve multiple energy conversion steps, leading to energy losses and reduced overall efficiency.
Lower Infrastructure and Deployment Costs
Establishing the infrastructure for hydrogen fueling stations is a significant undertaking. New stations are costly and time consuming to set up. The average capital cost required to set up a station is $1.9 million and for some, can exceed $4 million. In contrast, wireless charging infrastructure to power lithium-ion batteries is cost effective, easy to set up, and can be integrated seamlessly into existing facilities. Chargers can be placed wherever they’re needed throughout a facility, sometimes without any infrastructure changes and sometimes with minor electrical setup needed, such as adding a new drop. For industrial fleets looking to transition to cleaner energy sources without a massive upfront investment in time, money, and space, wireless charging and lithium-ion batteries are the best solution.
More Charging Flexibility and Higher Uptime
Wireless charging eliminates charging downtime because chargers can be placed where vehicles are working and charging begins within 2 seconds of vehicles pulling into range. No manual effort is required to keep fleets powered. Vehicles can charge during planned stops without the need for human intervention, ensuring they are always ready for operation when needed. Since charging starts as soon as a vehicle is within range, vehicles can get a partial charge wherever they stop and not just when longer breaks or shift changes occur. Hydrogen fueling stations, on the other hand, require more complex and manual refueling processes that cause downtime and operational disruptions. Stations have to be located in dedicated areas which means time is wasted simply driving to them, and the refueling process works like a traditional gas station where the operator has to spend 3-5 minutes manually refueling the vehicle. Because of this, hydrogen only makes sense for operations that don’t run continuously, as the disruption of needing to refuel is too costly for high volume, continuous operations.
No Manual Intervention to Charge
As noted above, to wirelessly charge lithium-ion batteries operators or AGVs simply need to pull within the parking range of a wireless charger and charging starts automatically. Hydrogen fuel cells, on the other hand, require manual refueling which is time consuming and takes time away from revenue generating activities, such as order fulfillment. Refuel compliance is also a major source of frustration for fleet managers as operators have to remember to refuel their trucks, typically once or twice a shift, and often forget, causing trucks to run out of fuel and need to be towed.
Lower Maintenance Costs
Hydrogen fuel cells are essentially electric vehicles with fuel cells instead of battery packs. So to compare maintenance costs, it’s important to compare the costs of maintaining the charging infrastructure, such as refueling hydrogen charging stations, and the costs of maintaining the fuel cells and batteries themselves. One of the biggest differences between fuel cells and lithium-ion batteries is the cooling system. Hydrogen systems use extremely pure water which requires filtration. The ion exchange filter that removes various contaminants must be replaced every 20,000 miles or so. Separately, hydrogen fuel cells are refueled by a hydrogen charging station that also needs to be refilled, and because hydrogen is stored in metal tanks, there is simply more equipment with hydrogen that needs to be maintained vs. with lithium-ion batteries and wireless charging. Lithium-ion batteries do not require scheduled cycling to maintain their battery life. When paired with all-solid-state wireless charging, which has no moving parts to wear out, fray, or break, lithium-ion batteries are the lowest maintenance motive power solution.
Better Environmental Impact and Sustainability
While hydrogen fuel cells produce water as their primary emission, the production, storage, and distribution of hydrogen often involves processes that generate carbon emissions. Lithium-ion batteries, when paired with clean energy sources, offer a more direct path to reducing overall greenhouse gas emissions. The environmental impact of battery production is a consideration, but advancements in recycling and sustainable mining practices are helping mitigate these concerns. In addition, because wireless charging enables vehicles to be charged while they work, such as at loading docks, wireless charging enables smaller batteries that can keep vehicles running.
Greater Technological Maturity and Support
Lithium-ion battery technology has matured significantly over the years, benefiting from extensive research, development, and market adoption. Wireless charging technology has also made substantial strides: Resonant Link’s 19.2 kW, 400 A wireless lift truck charger is currently being used by the top forklift manufacturers in the U.S. and has seen demand continue to grow since being introduced to the market. In contrast, hydrogen fuel cells are still in the early stages of development and face challenges related to production, storage, and distribution. Opting for technologies like lithium-ion batteries and wireless charging ensures reliability and ease of integration into existing fleet operations instead of the significant operational changes and re-training that a switch to hydrogen fuel cells would bring.
Conclusion
While hydrogen fuel cells are a promising technology for some applications like remote facilities with less reliable access to the grid, the practical and efficient solution for powering industrial fleets in warehouses today is leveraging lithium-ion batteries and wireless charging. The superior energy density, high efficiency, low infrastructure cost, and charging flexibility of wireless charging and lithium-ion batteries make this pairing an ideal choice for businesses seeking to enhance sustainability without compromising on operational efficiency. Fuel cell forklifts and lithium-ion batteries both offer long runtimes and rapid refueling, but hydrogen requires significant and costly infrastructure and manual refueling, which limits operations.
As we navigate towards a greener future, lithium-ion batteries and wireless charging stand out as the reliable and pragmatic choice for powering industrial fleets. Contact us today to learn how to get started.