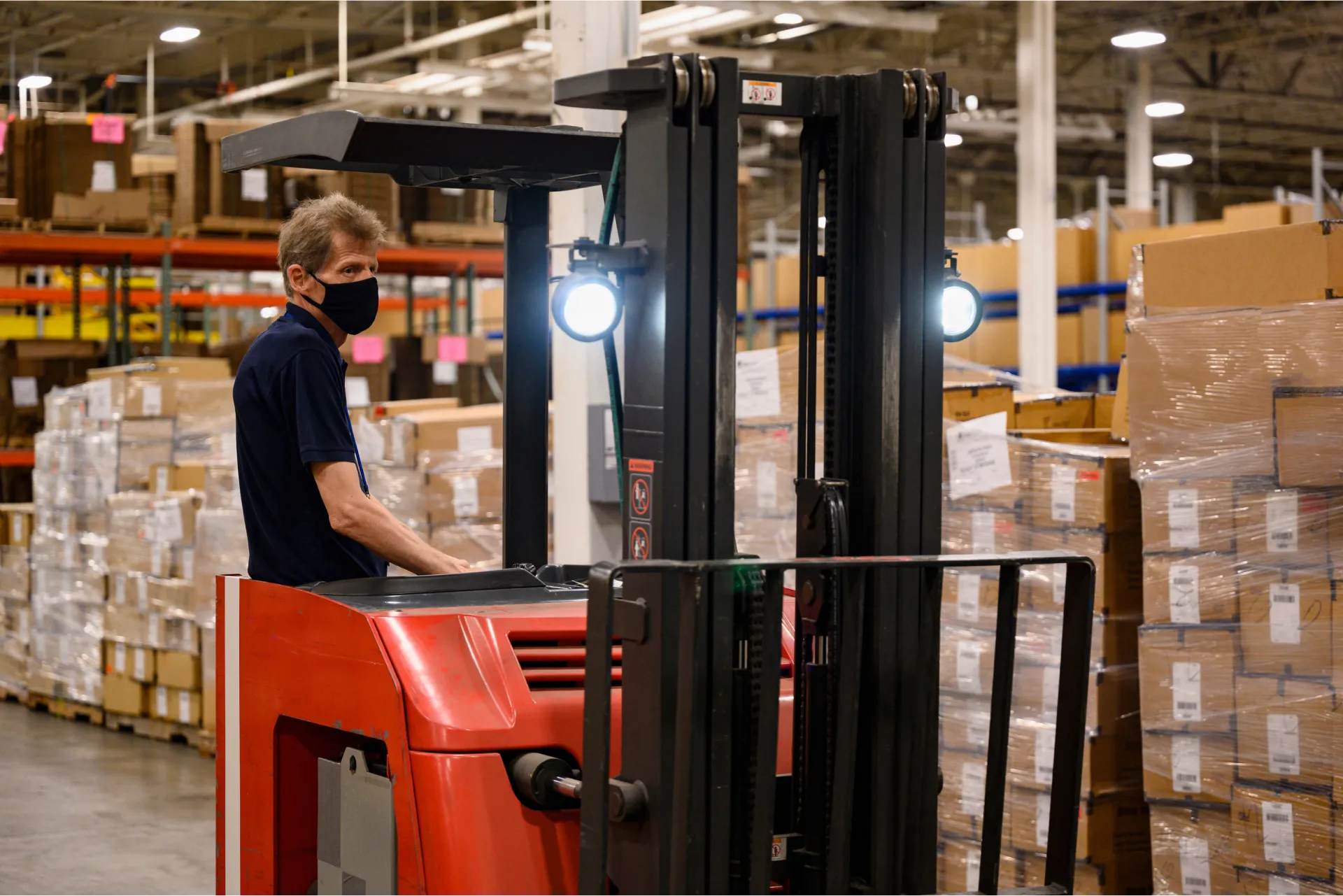
It’s no secret that warehouses are tough places to work. In 2021, the rate of warehouse injuries rose 5%. In addition to the personal harm they cause, warehouse injuries cause an average of weeks of lost work each, creating a domino effect. Injuries from repetitive and manual tasks are common and cause more time away from work than the average for injuries and illness. Forklift injuries are even worse, leading to 42% more time away from work than the average nonfatal injury or illness. Everyday, companies are working on new ways to keep workers safe, but technologies exist today that can immediately improve warehouse safety.
Continue reading to learn about 5 technologies that are essential to improve warehouse safety and that you can be using today to protect your workers and your business.
1. Automation and robotics
Automation and robots have been a hot topic for years. Like many technologies, however, they can seem more like buzz words than practical solutions, and because of that, many are uncertain what the pace of automation adoption in the coming years will really look like, especially for smaller companies that don’t have the budgets and scale of Amazon. This year’s Material Handling Institute Annual Industry Report predicts a 50% increase in adoption of robotics in warehouses over the next five years. 74% of supply chain leaders surveyed say they are increasing their technology investment to address workforce shortages, and to improve supply chain resiliency, transparency, and sustainability, and much of that investment is earmarked for automated solutions.
There’s an opportunity to use automation and robotics to do more too, as Sheheryar Kaoosji, executive director of the Warehouse Worker Resource Center, explains. “Technology can make jobs more secure and safer, but the industry is too focused on using it as a cost-saving measure.” One way to improve safety is to automate or altogether eliminate manual and repetitive tasks using robots. A leading cause of warehouse injuries are musculoskeletal injuries caused by repetitive motions. It’s an area on which Amazon is focusing a lot of attention.
There are several solutions on the market today from companies like Locus Robotics, Agility Robotics, and Bastian Solutions to name a few. They automate order picking, as an example of where much of the repetitive manual tasks occur in warehouses today. But companies need to view these technologies as necessary to make warehouses safer, and not just as solutions to save money. The reality is that what makes warehouses safer is also good for business, keeping people working and attracting those looking for better conditions.
2. 5G and reliable connectivity
The warehouse of the future – smart, efficient, and safe – depends on a more sophisticated power infrastructure, with wireless and 5G networks enabling a fleet of machines and operators to effortlessly communicate 24/7. 5G refers to the 5th generation mobile communications network, which offers speeds up to 100 times faster than 4G, is more reliable, can carry data at greater speeds with lower inactivity, and uses less energy. In fact, 5G equipment consumes only 10% of the energy consumed by 4G equipment.
Transitioning to 5G is essential for warehouses to become more sustainable, profitable, and safer, transforming both how warehouses operate and our supply chain as a whole. The real-time data capabilities alone will allow for better monitoring and management of issues, including safety indicators such as when somebody is slowing down and potentially becoming fatigued and at higher risk of an injury. Understandably, data privacy needs to be front and center in our transition to 5G, and the potential benefits if done correctly are immense.
One consideration with 5G is although infrastructure changes are needed to deploy 5G, especially when setting up private 5G networks, moving to 5G can actually simplify your warehouse infrastructure. With 4G and Wi-Fi, dense racking can create unwanted interference and dead zones so more access points are needed to ensure reliable connectivity. That’s not the case with 5G. In fact, in some situations, 5G has reduced the access points by nearly half.
3. Wireless charging
Any way you look at it, powering a fleet involves risks. With gas-powered fleets, carbon monoxide poisoning and refuel hazards create safety risks, among others. For an all or partially electric-fleet, wired charging and battery swapping cause injuries from the manual labor needed to swap batteries, dropped batteries and lead acid battery spills, and shocks and burns from melted cables and connectors.
Wireless charging solves these problems by eliminating the need for battery swapping and plugging-in while enabling efficient electric fleets. In addition to being the fastest and easiest-to-use, our wireless charging for material handling equipment was designed to be the safest motiv power charging option, period. Our object detection system recognizes objects that are already in the charge field and as they enter the charge field, and instantly stops charging or will not begin charging. Because of this, there is no opportunity for prolonged exposure or danger of objects heating. And without having to lift anything or plug anything in to make sure a vehicle’s battery is charged, our wireless charging is the safest option available.
4. Intelligent sensors and networked systems
Similar to the above, to enable Industry 4.0, or the fourth industrial revolution that leverages increased interconnectivity and smart automation for highly efficient logistics processes, intelligent sensors and networked systems are also needed. An intelligent sensor is a sensor that performs a function or series of functions once a certain condition is present. A networked system refers to a system of interconnected devices that exchange data and share resources with each other. Together, intelligent sensors and networked systems can detect the need for and then carry out complex processes. They allow logistics processes to be controlled and optimized in real time. Tracking packages is one example, but another example that is key to improving warehouse safety is vehicle, goods, and worker protection through collision avoidance. Collision avoidance for manned and autonomous vehicles leverages camera, RFID and laser technologies (Light Detection and Ranging or LiDAR for short) to look for obstacles, avoid collisions, collect navigation-related information from the operating environment, and send that information where it’s needed, for example, to a remote operator. SICK is one of the leaders in this area and has been making intelligent products to improve warehouse safety for years.
5. Augmented reality
Augmented reality is not a new concept. Augmented Reality, or AR, is an interactive experience that blends digital information like visuals and audio with a user’s actual environment in real time. An example is doing a job while wearing an AR headset that shows you how to do that job using visual cues. Companies like DHL have successfully demonstrated increases in productivity using augmented reality and smart glasses; however, AR is also growing in popularity as a training and safety tool.
Because turnover in warehouses is high, training is ongoing. Training new employees and re-training current employees is time intensive and it doesn’t always happen. Even when it does, some processes are so complex that it’s difficult for anyone to remember everything that needs to happen, which can cause safety issues for processes like battery swapping, as described above. AR addresses this challenge by providing true on-the-job training. AR devices can provide real-time, line-of-site instructions to employees to help them carry out tasks safely, and without necessarily needing prior training.
These are just a few of the technologies available now to improve warehouse safety. What’s your favorite? Send us a note to share what you’re doing to improve warehouse safety and we'll share it with our readers.